Corrugated boxes are the backbone of modern packaging logistics. They offer a cost-effective, durable, and scalable solution across industries—from e-commerce to industrial equipment.
This corrugated box buying guide provides a comprehensive understanding of corrugated packaging, from structure and manufacturing to types, sustainability, and purchasing considerations. Whether you’re sourcing boxes in bulk or customizing packaging for fragile goods, this guide offers the technical and practical knowledge to support an informed decision.
What Is a Corrugated Box? Definition, Structure, and Key Components
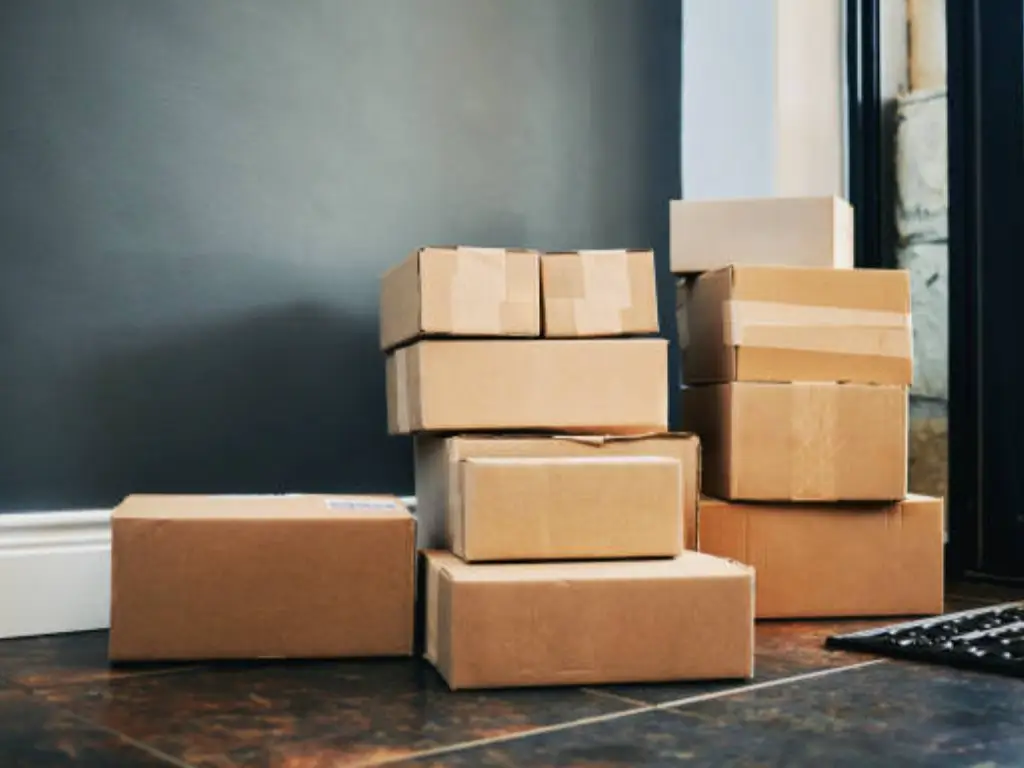
To understand the function and value of corrugated packaging, it’s essential to first grasp the corrugated box meaning. A corrugated box is a container made from corrugated fiberboard, which consists of three primary components:
- Linerboard: The flat outer surface of the board, typically made from virgin kraft or recycled paper.
- Flute (corrugated medium): The wavy layer placed between linerboards, available in various thicknesses and strengths.
- Board construction: Can be single-wall (one flute layer), double-wall (two flutes), or triple-wall (three flutes), depending on the required durability.
This structure creates a lightweight yet durable solution for protecting goods in transit.
Cardboard vs Corrugated: Key Differences in Structure and Use
Feature | Cardboard (Paperboard) | Wellkasten |
Structure | Single-layer, dense paper sheet | Multi-layer: linerboard + fluted medium |
Strength | Low rigidity, easily bent | High strength, impact-resistant |
Typical Use | Cereal boxes, cartons, cosmetic packaging | Shipping boxes, protective packaging |
Weight Capacity | Light-duty items | Medium to heavy-duty goods |
Manufacturing Purpose | Retail appearance, print quality | Transportation, storage, protection |
How Are Corrugated Boxes Made? From Paper to Finished Box
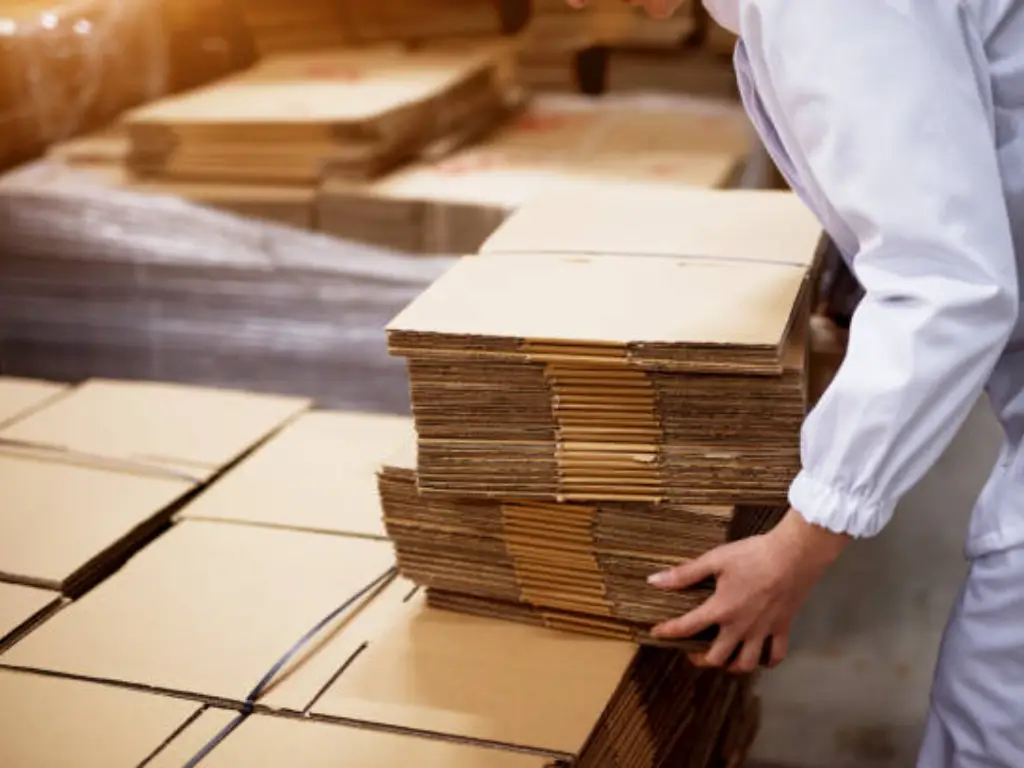
Understanding how corrugated boxes are made is key to evaluating their structural integrity, sustainability, and cost. The manufacturing process involves several critical steps, each governed by precise control parameters and industry standards.
1. Raw Material Preparation
Corrugated production begins with kraft paper, typically made from virgin or recycled wood pulp. The paper is processed into two grades: linerboard (used for the outer and inner faces) and corrugating medium (used to form the flutes). Pulp refining, drying, and calendaring ensure proper thickness and surface quality.
2. Corrugation Process
The corrugating medium is passed through heated, grooved rollers that form the characteristic fluted structure. These flutes are immediately bonded to one or two linerboards using starch-based adhesive, which is activated by steam.
3. Board Lamination
Depending on the box type, multiple layers of fluting and liners are laminated to create the required strength. Automated alignment systems prevent misregistration, ensuring uniform board thickness and performance.
4. Conversion: Drucken, Cutting, and Folding
Large sheets are printed using flexographic presses (for logos, handling instructions, or barcodes), then die-cut or slotted into predefined shapes. Scoring and folding lines are applied for easy assembly.
5. Box Assembly and Palletization
Finished blanks are folded, glued or stitched, and stacked flat. Quality checks ensure compliance with performance standards like FBA guidelines, ISO 9001, or ASTM D4727 before final palletization and delivery.
Types of Corrugated Boxes: Wall Constructions, Flute Grades, and Box Styles
Corrugated boxes vary widely in strength, cushioning, and cost-efficiency, depending on their wall construction, flute profile, and overall design. This section breaks down the most critical categories to help buyers match packaging structure to their intended use.
Wall Constructions: Single, Double, and Triple Wall
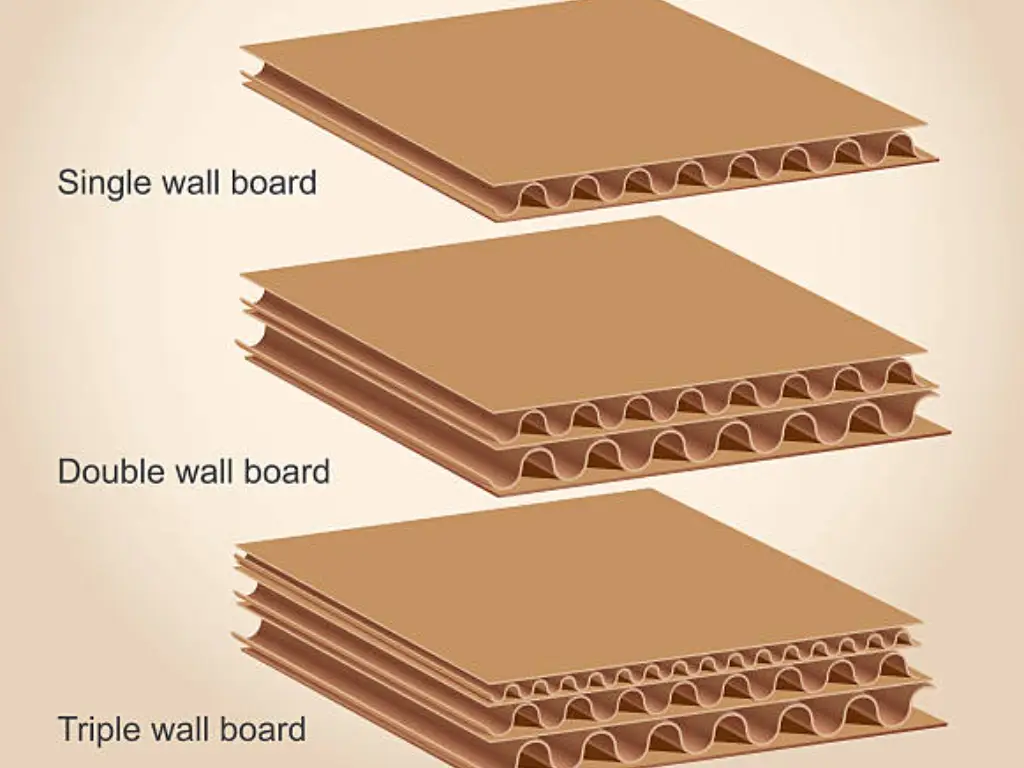
Corrugated board is available in single-wall, double-wall, and triple-wall formats.
- Single-wall corrugated board consists of one layer of fluting between two liners. It is lightweight and cost-effective, ideal for shipping consumer goods.
- Double-wall includes two fluted mediums and three liners. It significantly improves stacking strength and puncture resistance, commonly used in industrial packaging and export cartons.
- Triple-wall comprises three flutes and four linerboards, offering strength comparable to wooden crates. It’s used for extremely heavy or bulky items in automotive and machinery shipments.
Each increase in wall thickness enhances the box’s resistance to compression and moisture, but also adds weight and cost—requiring careful trade-off analysis.
Flute Grades: A, B, C, E, and F
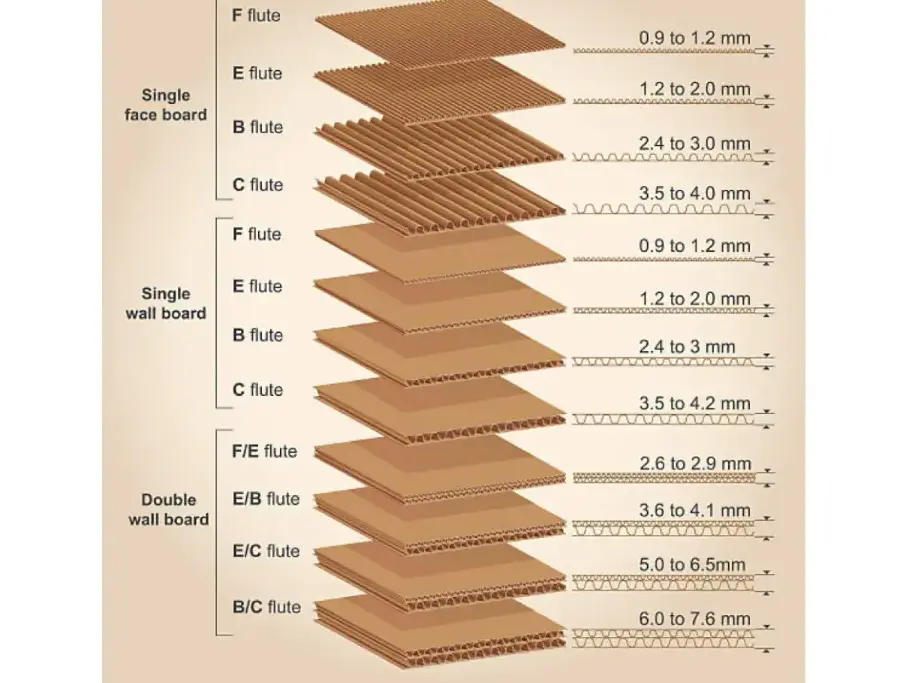
Flute type impacts both structural strength and packaging aesthetics. Below is a comparison:
Flute Type | Thickness | Strength | Common Use |
A Flute | ~4.5 mm | Excellent cushioning | Fragile items |
B Flute | ~3.2 mm | High crush resistance | Food trays, retail packs |
C Flute | ~3.9 mm | Balanced performance | General shipping boxes |
E Flute | ~1.6 mm | Great print surface | Retail & custom packaging |
F Flute | ~0.8 mm | Thin, fine finish | Small-format retail boxes |
Generally, C-flute is most commonly used for general shipping, while E- and F-flutes are preferred in applications where visual presentation and compactness matter. A- and B-flutes are ideal for protection and rigidity, especially in stacked configurations.
In double-wall constructions, the most common flute combinations are:
- BC flute: Combines B-flute (high crush resistance) and C-flute (balanced cushioning and stacking strength). It’s widely used for industrial packaging and export cartons.
- EB flute: Combines E-flute (thin, printable) with B-flute. This pairing offers both structural strength and superior surface for branding—ideal for heavy retail products or fragile goods.
- AC flute: Offers maximum cushioning and stacking performance, used for high-value, heavy, or vibration-sensitive items.
For triple-wall boards, a typical configuration is ACA or BAC, balancing compression strength, cushioning, and rigidity. These combinations are chosen based on the required performance in heavy-duty logistics, and can reach strength ratings comparable to wooden crates.
Box Styles: RSC, FOL, HSC, Die-Cut, and Telescopic
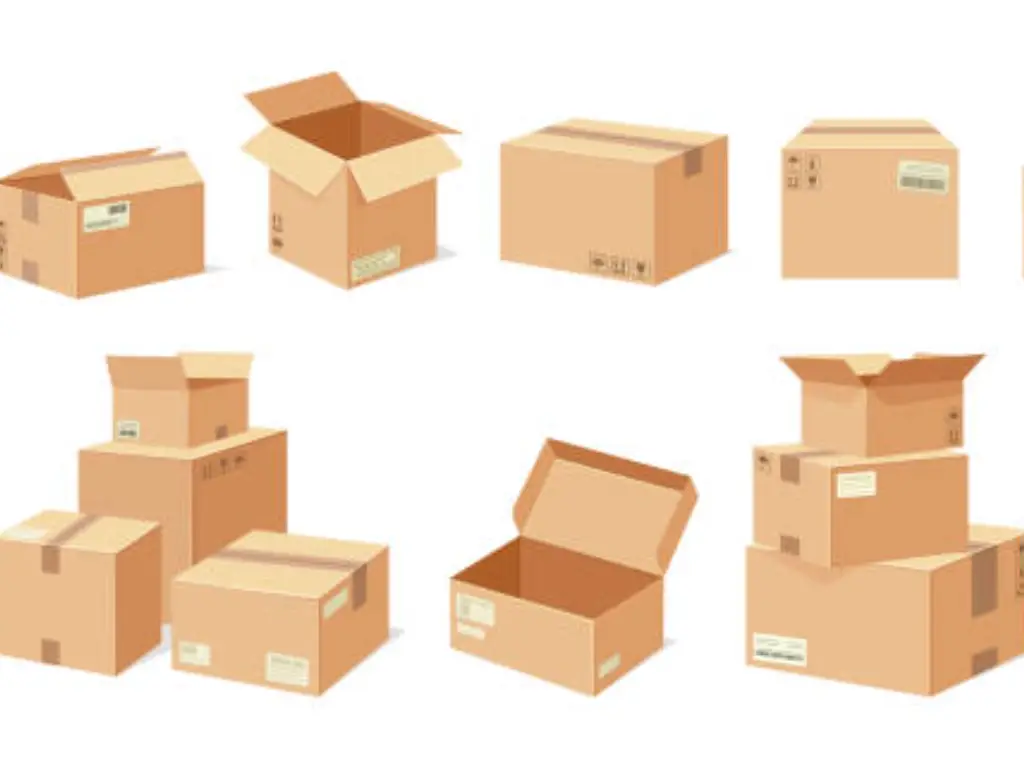
Box style determines how the board is cut, folded, and assembled—each serving a different purpose.
- RSC (Regular Slotted Container): The most common box style, with flaps of equal length that meet in the center. It’s cost-effective and efficient for most automated packaging lines.
- FOL (Full Overlap Slotted Container): The outer flaps fully overlap, offering extra strength on the top and bottom. Ideal for heavier goods requiring added bottom support.
- HSC (Half Slotted Container): Similar to RSC but with an open top, used for products that require easy access or shelf-ready display. Often combined with a lid.
- Die-Cut Boxes: Custom-cut using a steel die to fit exact product dimensions. These offer enhanced branding potential and are widely used in cosmetics, electronics, and retail.
- Telescopic Boxes: Consist of two parts—a top and bottom—that slide over each other. Best for long or irregularly shaped items, offering adjustable height and better strength distribution.
Choosing the right box style is critical in balancing structural performance, cost-efficiency, and functional needs. As part of this corrugated box buying guide,
Common Uses of Corrugated Boxes Across Industries
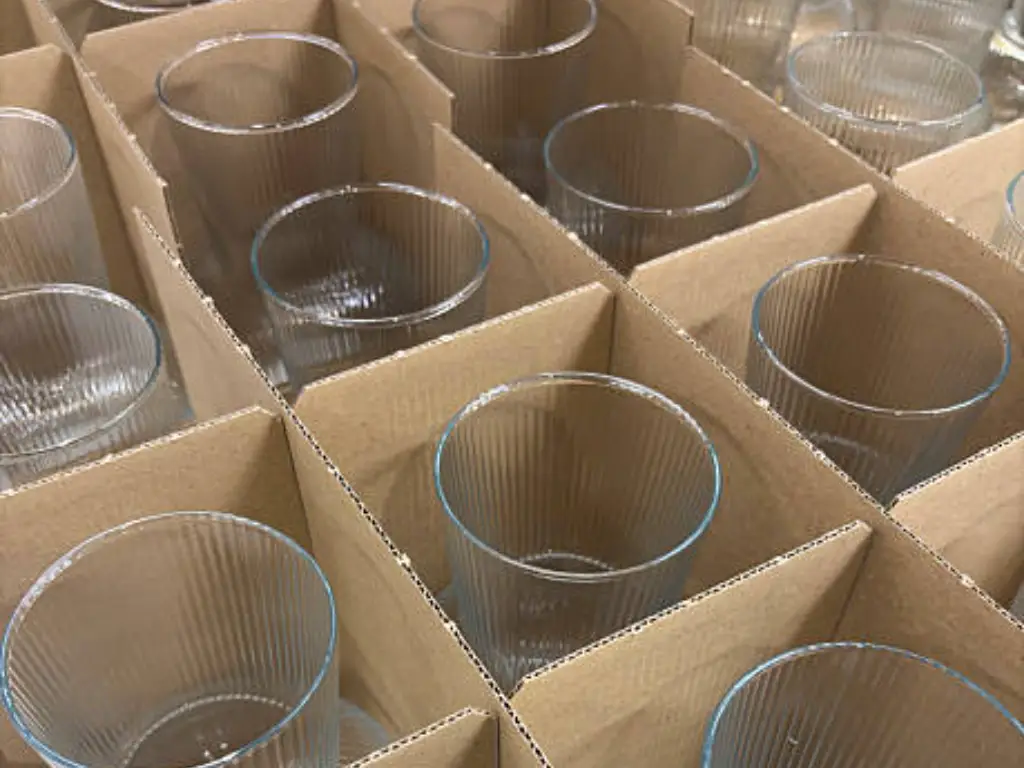
The uses of corrugated boxes span across industries due to their lightweight, customizable, and protective characteristics. Their adaptability makes them the default packaging solution in sectors including:
E-commerce and Retail
- Commonly use RSC boxes with custom branding.
- Lightweight and stackable for last-mile delivery.
- Often integrated with paper-based inserts for eco-conscious unboxing.
Industrial and Manufacturing
- Double or triple-wall corrugated boxes for shipping heavy machinery or tools.
- Reinforced FOL or pallet-ready formats for global freight.
Food and Agriculture
- Vented corrugated trays used for perishables.
- FDA-compliant liners or wax-coated boards for moisture resistance.
Medical and Pharmaceutical
- Custom die-cut inserts for vials or instruments.
- Printed instructions or compliance markings on outer box.
Exhibition and Display
- E-flute boxes used for high-resolution printed graphics.
- Often customized for point-of-purchase displays.
Whether protecting fragile glassware or showcasing retail products, the uses of corrugated boxes remain functionally diverse and industry-critical.
Are Corrugated Boxes Recyclable and Biodegradable? A Sustainability Overview
Corrugated boxes are among the most environmentally favorable packaging materials due to their high recyclability and natural biodegradability. However, these two terms are not interchangeable and involve different end-of-life processes.
- Recyclability: Most corrugated boxes are made of uncoated kraft paper or recycled fibers and are 100% recyclable. They can typically withstand up to 5–7 recycling cycles before fiber degradation affects quality. Boxes printed with water-based inks and assembled using starch adhesives pose no barrier to recycling. However, contamination with plastic coatings, waxed surfaces, or laminated film significantly reduces recyclability.
- Biodegradability:Corrugated fiberboard decomposes naturally in soil or composting environments, typically within 3–6 months under industrial composting conditions. Fully biodegradable options must avoid polymer additives, synthetic adhesives, or UV-cured inks. Certifications such as ASTM D6400 or EN 13432 help verify biodegradability for packaging materials.
In summary, while most corrugated boxes are both recyclable and biodegradable, buyers should verify specific coatings and adhesives with their supplier to ensure compliance with local recycling and composting systems. This due diligence supports responsible packaging choices aligned with environmental goals.
Final Considerations When Choosing Corrugated Boxes
Before placing an order, buyers must evaluate both structural integrity and supplier reliability.
Quality Testing and Compliance Standards
Reliable corrugated boxes are verified through standardized performance tests:
- Cobb Test measures water absorption to assess moisture resistance.
- Edge Crush Test (ECT) indicates stacking strength—critical for warehouse storage.
- Flat Crush Test (FCT) evaluates flute compression strength.
- Mullen (Burst) Test assesses puncture resistance under sudden pressure.
These tests are typically conducted in accordance with ASTM D642 or ISO 2759, and results should be traceable via box certification stamps.
Customization Factors to Consider
When requesting customized boxes, align structural specifications with use-case demands:
- Printing method (flexographic vs. digital)
- Surface treatments (wax, aqueous, or UV coatings)
- Functional features such as die-cuts, inserts, or ergonomic handles
These options affect not only aesthetics, but also protection, user experience, and cost.
Choosing a Reliable Supplier
An ideal supplier should offer:
- Certifications like ISO 9001, FSC, or PEFC
- In-house design support and material traceability
- Fast sampling, strong compliance knowledge, and scalable production capacity
This final stage of the corrugated box buying guide ensures your procurement decisions align with performance, sustainability, and commercial objectives.
Packccp holds ISO 9001 and FSC certifications, offers OEM custom packaging for brands like Disney, and is known for delivering reliable quality and flexible corrugated solutions.
Start your packaging project with a trusted partner—contact us today to explore tailored corrugated solutions that meet your performance, sustainability, and branding goals.